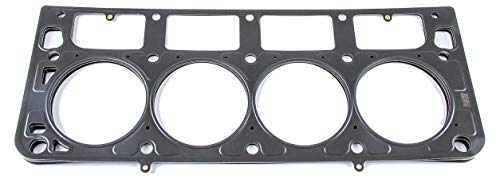
Wedge compression back gasket is a crucial component in various industries, including automotive and aerospace. It is responsible for maintaining the seal between two surfaces while accommodating any minor misalignments or deformations. Precision is key in these applications, and measuring the wedge compression back gasket accurately is essential for optimal performance.
When measuring the wedge compression back gasket, several key parameters need to be considered. These include the thickness, width, and height of the gasket. The thickness is typically measured using specialized tools such as micrometers or calipers, ensuring an accurate reading. The width and height can be measured using similar tools, taking into account any irregularities or deformations that may affect the overall dimensions.
It is important to note that the method of measurement may vary depending on the specific requirements of the application. For instance, in automotive manufacturing, the thickness, width, and height of the wedge compression back gasket may need to be measured at multiple points along its length to ensure consistency and uniformity. This is especially crucial when dealing with high-pressure systems or critical sealing applications.
Additionally, the material properties of the wedge compression back gasket should also be taken into consideration. The hardness, elasticity, and compression characteristics of the gasket can significantly impact its sealing performance. Measuring these properties accurately can be done using specialized equipment that applies controlled compression or indentation tests. These tests help determine the gasket’s ability to maintain a seal and withstand the forces it will be subjected to during operation.
Overall, measuring the wedge compression back gasket accurately is essential for ensuring its optimal performance and longevity. By considering the dimensions and material properties, engineers and manufacturers can select the most suitable gasket for their specific applications, guaranteeing a reliable seal that meets the highest quality standards.
Understanding the Importance of Gasket Compression
Gasket compression is a critical factor to consider when assessing the effectiveness and efficiency of a wedge back gasket. Proper compression ensures a reliable seal against leaks, prevents fluid or gas escape, and maintains structural integrity under varying conditions. It plays a crucial role in the overall functionality and longevity of the gasket.
When a gasket is compressed, it is forced against the mating surfaces, creating a tight seal. This compression ensures that any imperfections or irregularities on the mating surfaces are filled, preventing leaks and providing a secure barrier. Without proper compression, the gasket may fail to effectively seal, resulting in potential leaks, system inefficiencies, and safety risks.
There are several key reasons why gasket compression is important:
- Sealing Effectiveness: Proper compression ensures that the gasket conforms to the mating surfaces, eliminating any potential gaps or voids. This tight seal prevents the passage of air, liquid, or gases, maintaining system integrity and preventing leaks.
- Load Distribution: Compression helps distribute the load evenly across the gasket. By applying pressure, the gasket is able to support the mating surfaces and withstand external forces, preventing deformation and maintaining its shape. This load distribution improves the overall durability and performance of the gasket.
- Tolerance Compensation: Compression compensates for any surface irregularities, imperfections, or variations. By compressing the gasket, it fills any gaps or voids, ensuring a secure seal. This tolerance compensation is vital in applications where the mating surfaces may not be perfectly smooth or aligned.
- Vibration and Thermal Resistance: Proper compression helps the gasket absorb and distribute vibrations and thermal expansion. It allows the gasket to flex and adjust to changing conditions, preventing damage and prolonging its lifespan. The ability to withstand these external factors is particularly important in industrial applications.
- Longevity and Reliability: Effective compression ensures that the gasket remains secure and intact over an extended period. It prevents premature failure, reduces maintenance costs, and improves the overall reliability of the system.
In conclusion, understanding the importance of gasket compression is crucial for ensuring a reliable and efficient sealing solution. Proper compression enables the gasket to effectively seal against leaks, distribute loads, compensate for surface irregularities, withstand vibrations and thermal expansion, and ultimately provide longevity and reliability. When measuring wedge compression back gaskets, ensuring the appropriate compression is achieved is vital for optimal performance and functionality.
Measuring Tools
In order to accurately measure wedge compression back gasket, you will need to use the right tools. Here are some common measuring tools that can be used for this purpose:
Tape Measure
A tape measure is a flexible ruler that can be used to measure the length and width of the gasket. It is important to ensure that the tape measure is straight and not twisted when measuring the gasket to get accurate results.
Calipers
Calipers are a precision measuring tool that can be used to measure the thickness of the gasket. There are different types of calipers available, including digital calipers and vernier calipers. Make sure to use the appropriate type of calipers for accurate measurements.
When measuring the gasket with calipers, gently close the jaws around the gasket and take the measurement from the display. Be careful not to squeeze the gasket too tightly as it may compress and give incorrect measurements.
It is also important to clean the measuring surfaces of the calipers before taking measurements to avoid any dirt or debris that may affect the accuracy of the measurement.
Using these measuring tools properly and ensuring accurate measurements will help in determining the compression of the back gasket and ensuring a proper fit. This will ultimately contribute to the overall effectiveness and durability of the gasket.
Choosing the right tools for accurate measurement
Measuring wedge compression back gasket is a task that requires precision and attention to detail. To ensure accurate results, it is important to choose the right tools for the job. Here are some key considerations when selecting tools for measuring wedge compression back gasket:
1. Vernier Caliper
A vernier caliper is a versatile tool that can measure the thickness and width of the gasket. It provides precise measurements with its fine scale and adjustable jaws, allowing for accurate and repeatable readings. Make sure to select a caliper suitable for the size of the gasket being measured.
2. Micrometer
A micrometer is ideal for measuring the thickness of the gasket. It offers higher precision than a vernier caliper and is capable of measuring within a thousandth of an inch. When using a micrometer, ensure that it is properly calibrated and choose the appropriate measuring faces for the task.
3. Gasket Thickness Gauge
A gasket thickness gauge is specifically designed for measuring the thickness of gaskets. It provides quick and reliable measurements in a range of thicknesses. Look for a gauge that has a broad measurement range to accommodate various gasket sizes.
In addition to these specific tools, it is also important to have a clean and well-lit workspace to facilitate accurate measurements. Avoid any external factors that could affect the measurements, such as excessive temperature or vibrations.
When measuring wedge compression back gasket, it is crucial to take multiple measurements and calculate an average to account for any variations. This will help ensure that the measurements are accurate and provide a reliable basis for further analysis.
By using the right tools and following proper measurement techniques, you can obtain accurate and reliable measurements of wedge compression back gasket, crucial for their proper installation and performance.
Step-by-Step Guide
Measuring the compression of a wedge back gasket is a simple process that can be done with a few steps. Here is a step-by-step guide to help you along the way:
- Gather the necessary tools: Before you begin, make sure you have all the tools you need to measure the wedge compression back gasket. This may include a ruler, calipers, or a measuring tape.
- Prepare the gasket: Ensure that the wedge back gasket is clean and free from any debris or dirt that might affect the accuracy of the measurement. Wipe it down with a clean cloth if necessary.
- Position the gasket: Place the wedge back gasket on a flat surface with the compressed wedge facing upwards. Make sure it is positioned securely and does not move during the measurement process.
- Measure the width: Use your ruler, calipers, or measuring tape to measure the width of the compressed wedge back gasket. Take measurements at multiple points to ensure accuracy.
- Record the measurements: Note down the measurements you have obtained for the width of the compressed wedge back gasket. This will serve as your reference for future use.
- Repeat the process: If you need to measure multiple wedge compression back gaskets, repeat steps 3 to 5 for each gasket.
- Analyze the measurements: Compare the measurements you have obtained to the specifications provided by the manufacturer or industry standards. This will help determine if the compression of the wedge back gasket is within the acceptable range.
Following these steps will ensure that you accurately measure the compression of the wedge back gasket and can make informed decisions about its usage or replacement.
Measuring the wedge compression back gasket
The wedge compression back gasket is an important component in various mechanical systems, especially those that require a tight seal to prevent leaks. In order to ensure its proper functioning, it is crucial to measure the wedge compression back gasket accurately. This can be done using the following steps:
Step 1: Gather the necessary tools
Before starting the measurement process, make sure you have the right tools at hand. This usually includes a ruler or caliper for taking precise measurements, as well as any additional equipment specific to your gasket and system.
Step 2: Remove the gasket
Carefully remove the wedge compression back gasket from its position in the system. Pay attention to any specific instructions or precautions provided by the manufacturer to avoid damage or misalignment.
Step 3: Clean the gasket
Thoroughly clean the gasket using an appropriate solvent to remove any dirt, grease, or debris that may affect the accuracy of your measurements. Ensure that the gasket is completely dry before proceeding.
Step 4: Measure the dimensions
Using a ruler or caliper, measure the key dimensions of the wedge compression back gasket. These typically include the outer diameter, inner diameter, and thickness. Take multiple measurements at different points to ensure accuracy, and record the values.
Step 5: Analyze the measurements
Once you have obtained the measurements, analyze them to ensure they fall within the specified tolerances. Compare the recorded values to the manufacturer’s specifications to determine if the gasket is within acceptable limits or if it needs to be replaced.
By following the above steps, you can effectively measure the wedge compression back gasket and ensure that it meets the required standards for optimal performance in your mechanical system.
Analyzing the Results
Once you have completed the wedge compression back gasket testing, it is important to analyze the results to determine the effectiveness and performance of the gasket. This analysis will allow you to make informed decisions about whether the gasket meets the required specifications and standards.
1. Measure Compression: The first step in analyzing the results is to measure the compression of the gasket. Use a micrometer or caliper to measure the thickness of the gasket before and after compression. Calculate the percentage of compression by dividing the difference in thickness by the original thickness and multiplying by 100.
2. Compare Compression Data: Next, compare the compression data of the gasket to the required specifications and standards. Determine if the compression percentage falls within the acceptable range. If the compression is too low, it may indicate a poor sealing performance, while excessive compression could lead to damage or leakage.
3. Evaluate Leakage: Additionally, evaluate the occurrence of any leakage during the compression test. If there is any sign of leakage, determine its source and location. This will provide insights into the potential points of failure and help identify any design or manufacturing issues.
4. Consider Material Properties: Take into account the material properties of the gasket, such as its hardness, elasticity, and resistance to temperature and chemicals. Assess whether the gasket is suitable for the intended application and if it can withstand the required conditions without degradation or failure.
5. Compare with Previous Tests: If available, compare the results of the current test with previous tests conducted on similar gaskets or materials. Look for any trends or patterns that may indicate consistent performance or issues that need to be addressed.
6. Take External Factors into Account: Lastly, consider any external factors that may have impacted the results, such as the testing environment, equipment calibration, or operator technique. These factors can affect the accuracy and reliability of the results and should be taken into consideration during the analysis.
By carefully analyzing the results of the wedge compression back gasket testing, you will be able to make informed decisions regarding the quality and suitability of the gasket for your specific needs.